Aluminum mold VS steel moldy
Hot keword :2024 5052 5083 6061 7075
Mold production and parts are completed in 15 days or less
Mold manufacturing cost is low, from the current stage of the mold market: aluminum alloy market is relatively stable than the steel market, more conducive to the implementation of cost budget control of enterprises. The aluminum mold is about 50% lighter than the steel mold, so the aluminum mold is more superior than the steel mold in the adjustment of the equipment in the manufacturing, installation and injection workshop. The transport of lightweight moulds eliminates the need for expensive lifting equipment such as cranes and lifting trucks, thus reducing manufacturing costs.
Rapid production of no more than 1,000~5,000 mold, product process is not harsh products. Generally used for quick proofing, small batch products. Production quantity up to 10,000 or more; Some molds are capable of producing hundreds of thousands of parts, depending on the material type and geometry.
Single cavity and multi-cavity die: 1 cavity, 2 cavity, 4 cavity and 8 cavity die can be used depending on part size and complexity.
Thermoplastic and thermosetting materials are the same as mass production materials; More than 100 different materials can be used, including ABS, PC, PP, LCP, POM and liquid silicone rubber.
If damaged, no maintenance costs and lifetime mold replacement, improve heat dissipation, no need to use messy cooling lines
The aluminum mold is easy to process, has high dimensional stability and excellent thermal conductivity, which can save the cooling time of the mold in production up to 50%. With the development of the market, the phenomenon of aluminum mold replacing steel mold is gradually appearing in the European and American markets.
what are the advantages of aluminum mold?
- Light weight. Because its density is only 36% of the general die steel, the motion inertia is relatively low, and it is easy to add and reduce the speed in the production process, which can reduce the loss of machine and die.
- Easy machining and high dimensional stability. The cutting speed is more than 6 times faster than that of ordinary die steel, so the die processing time is greatly reduced, so that the die can be produced faster.
- Excellent heat conductivity. Its thermal conductivity is higher than that of ordinary die steel, so the cold cutting time of the die can be saved by 50% during production, thus improving the production efficiency of the die. So aluminum mold in injection mold, blow mold, low pressure mold, rubber mold and other different mold industry 80% of the products are widely used. With the development of the market, super duralumin has replaced steel in the European and American markets
Features:
- High strength heat-treatable alloy.
- Good mechanical properties.
- Good usability.
- Easy to process, good wear resistance.
- Good corrosion resistance and oxidation resistance. Main Applications: Aviation fixtures, trucks, tower buildings, ships, pipelines and other applications in buildings requiring strength, weldability and corrosion resistance. Such as: aircraft parts, gears and shafts, fuse parts, instrument shafts and gears, missile parts jump valve parts, turbines, keys, aircraft, aviation and defense applications Hardness, density and mechanical properties of superdural alloy
The mold made of aluminum alloy has the following characteristics:
- good material uniformity: excellent heat treatment technology, the product in 300℃ thickness (diameter) below, strength, hardness basically maintain the same;
- high surface precision, reduce the waste of materials
- Good processing performance: the deviation of chemical composition, strength and hardness is reduced to a minimum, and the phenomenon of “sticking knife” and “breaking knife” is eliminated in processing;
- high-speed machining, almost no deformation: perfect pre-tensile (T651) process, completely eliminate internal stress, in processing and stress is not easy to warping, cracking and deformation;
- the material density is good: unique grain refinement process guarantee, no sand holes, transverse lines, bubbles and impurities;
- high temperature resistance: at 400℃ working environment will not occur permanent deformation;
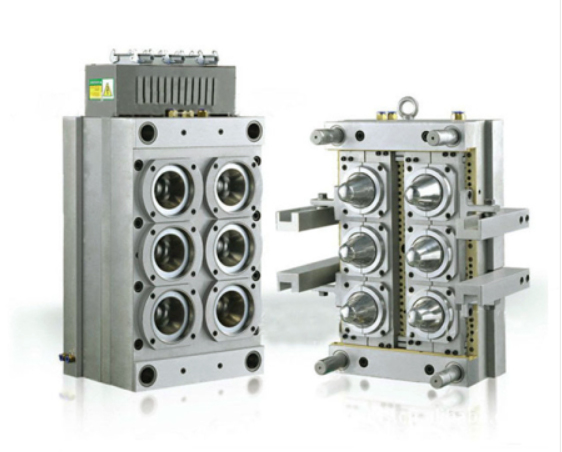